Positive displacement pumps
A positive displacement pump makes a fluid move by trapping a fixed amount and forcing (displacing) that trapped volume into the discharge pipe.
Some positive displacement pumps use an expanding cavity on the suction side and a decreasing cavity on the discharge side. Liquid flows into the pump as the cavity on the suction side expands and the liquid flows out of the discharge as the cavity collapses. The volume is constant through each cycle of operation.
The positive displacement pumps can be divided in two main classes
- reciprocating
- rotary
The positive displacement principle applies whether the pump is a
- rotary lobe pump
- progressing cavity pump
- rotary gear pump
- piston pump
- diaphragm pump
- screw pump
- gear pump
- vane pump
- regenerative (peripheral) pump
- peristaltic
Non-positive pump
Rotodynamic pumps (or dynamic pumps) are a type of velocity pump in which kinetic energy is added to the fluid by increasing the flow velocity. This increase in energy is converted to a gain in potential energy (pressure) when the velocity is reduced prior to or as the flow exits the pump into the discharge pipe.
Centrifugal and propeller pumps are examples of non-positive-displacement pumps. Like most pumps, a centrifugal pump converts rotational energy, often from a motor, to energy in a moving fluid. A portion of the energy goes into kinetic energy of the fluid. Fluid enters axially through eye of the casing, is caught up in the impeller blades, and is whirled tangentially and radially outward until it leaves through all circumferential parts of the impeller into the diffuser part of the casing. The fluid gains both velocity and pressure while passing through the impeller. The doughnut-shaped diffuser, or scroll, section of the casing decelerates the flow and further increases the pressure.
Difference between positive and non-positive displacement pumps:
- Pressure - Positive displacement pumps work for high pressure applications, pressure might be upto 800 bar. Non-positive displacement pumps are basically used for low pressure applications and are designed to work for a maximum pressure of 18 to 20 bar.
- Efficiency - In positive displacement pumps, efficiency increases with increasing pressure. Whereas in non-positive displacement pumps, efficiency peaks at best-efficiency-point. At higher or lower pressures, efficiency decreases.
- Viscosity - In positive displacement pumps, efficiency increases with increasing viscosity. On the other hand, efficiency of non-displacement pumps decreases with increasing viscosity due to frictional losses inside the pump.
- Performance - Flow is constant with changing pressure in a positive displacement pump whereas Flow varies with changing pressure in a non-positive displacement pump.
- Pressure vs Rate of Flow graph -
a. Positive displacement pump - The pump will displace the same amount of fluid on every revolution, regardless of system pressure.
Identical systems with one hardly working (1st Pic.) and one working hard (2nd Pic.). Both systems still displace the same amount of fluid.
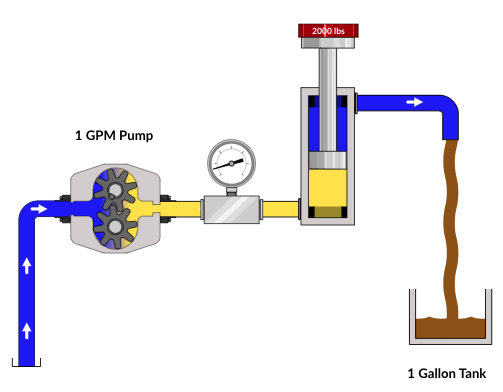
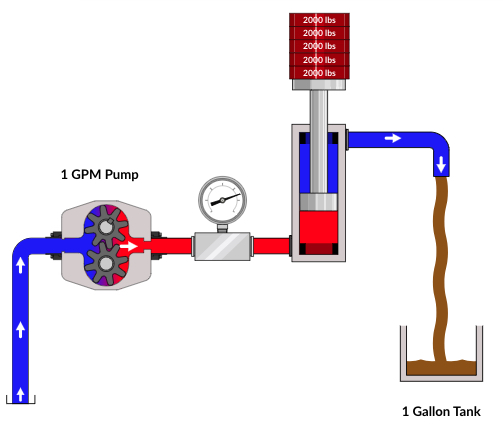
b. Non-positive displacement pump - A non-positive displacement pump's output flow rate changes in response to restriction (pressure) on the outlet.